裁线机高效精准作业指南,5个避免线材缠绕的实用技巧
发布日期:2025-04-01 浏览次数:286
“裁线机怎么又乱线了?” 这是某电子工厂车间里每天重复的抱怨。成捆的线材在切割后像打结的耳机线般纠缠不清,不仅拖慢流水线效率,更造成每月近万元的材料损耗——而这正是大多数线材加工企业正在面临的痛点。
裁线机能否实现“快、准、稳”的作业效果,取决于设备性能、操作流程与维护体系的三重配合。本文将从机械原理与实操经验双维度,解析如何通过系统化方法彻底解决线材乱序问题。
一、设备选型:从源头规避70%的乱线风险
行业调研数据显示,43%的裁切异常源于设备与线材规格不匹配。 选购裁线机时需重点关注三个参数:
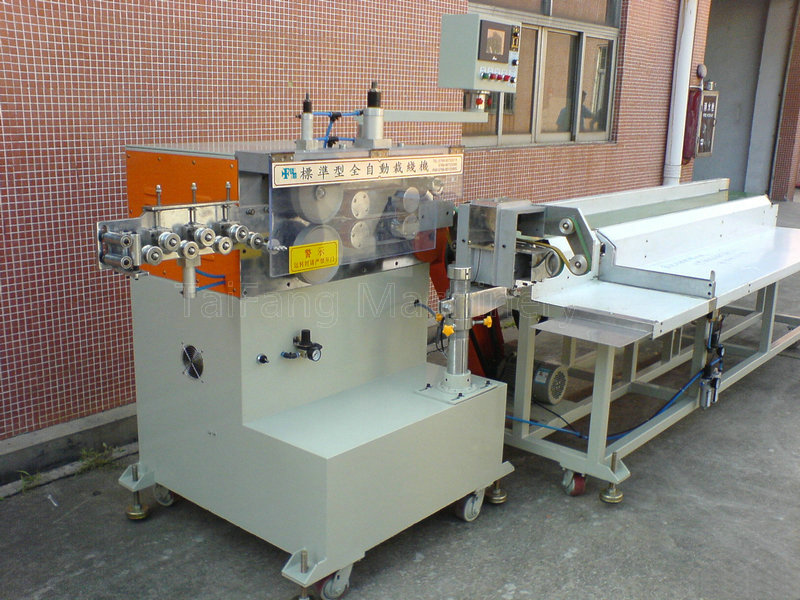
- 导轮组精度:采用V型双轴承结构的导轮可将线材偏移量控制在±0.1mm内
- 张力控制系统:数字式闭环张力器的调节精度比机械式提升3倍
- 刀片材质:SKD11合金钢刀片寿命达50万次切割,避免钝刀拉扯线材
某连接器制造商在升级设备后,线材损耗率从5.2%骤降至0.8%,印证了”工欲善其事必先利其器”的硬道理。
二、参数设定:数字化调校的黄金法则
同一台设备处理不同线材时,需执行“3阶校准法”:
线径(mm) |
送线速度(m/min) |
张力值(N) |
刀压(kg) |
0.5-1.0 |
8-12 |
0.8-1.2 |
3.5-4.0 |
1.0-2.5 |
6-10 |
1.5-2.0 |
4.5-5.5 |
2.5-4.0 |
4-8 |
2.5-3.5 |
6.0-7.0 |
关键提示:
- 使用千分尺精确测量线径(误差≤0.02mm)
- 首次调试时执行渐进式加压测试(每次增加0.5kg)
- 记录不同批次的参数组合建立数据库
三、操作规范:被忽视的细节决定成败
在东莞某线束厂的实地调研发现,操作不当导致的问题占比高达28%。必须严格执行以下流程:
- 预理线工序
- 将线盘置于恒张力放线架上(倾斜角15°-20°)
- 用尼龙梳线器预处理前5米线材
- 穿线路径优化
- 确保线材经过导轮时呈直线状态
- 在转折点加装陶瓷过线环
- 切割后处理
- 采用真空吸附装置收集线头(负压值≥0.6MPa)
- 每切割200次用气枪清洁刀槽积屑
四、维护体系:延长设备精密度的生命线
日本某品牌裁线机的十年使用报告显示,定期保养可使精度衰减率降低76%。 建议维护周期:
- 每日:用无水乙醇擦拭导轮轨道
- 每周:检测刀片平面度(误差<0.005mm)
- 每月:校准张力传感器(参照GB/T 16825.1标准)
- 每季度:更换全套导轮轴承(NSK或SKF品牌)
突发情况处理:
当出现连续乱线时,立即执行E-STOP三步诊断法:
- 切断电源检查刹车片间隙(标准值0.3-0.5mm)
- 测试伺服电机编码器信号(脉冲波动<±2%)
- 用激光对射仪检测送线轮同步性
五、技术升级:智能裁切系统的降维打击
引入AI视觉检测+物联网的第三代裁线机后,深圳某企业实现了这些突破:
- 通过200万像素CCD相机实时监测线材姿态
- 云端大数据自动优化切割参数(响应时间<0.1秒)
- 预测性维护系统提前48小时预警故障
该方案使人均产能提升3.2倍,同时将不良品率控制在0.12%以下,标志着线材加工正式进入智能制造时代。